摘要:液位测量及控制是自动化技术的重要组成部分,准确可靠的液位测量对装置的平稳运行及安全生产起着十分重要的作用。通过引用四个具体案例即抽余液分馏塔开车过程中发生爆炸、溶剂回收塔操作不稳定、锅炉汽包液位控制不稳定、分液罐玻璃板液位计读数不准确,详细说明了假液位对装置操作和安全生产带来的危害,分析了这些假液位产生的原因,并提出了相应的处理措施:在进料或操作条件改变时,应及时通过分析化验取得被测液体密度变化情况,并修正差压液位计差压信号;采用在塔釜和塔顶间设差压计、在塔釜分段设玻璃板液位计等方法可对虚假液位或起泡进行有效辨别;仪表管口位置应避免受流入、流出介质的冲击,无法避开时应设防冲挡板;采用三冲量控制方案可有效地解决锅炉汽包假液位引发的控制问题;所测量设备的玻璃板液位计或差压液位计上下仪表管口间的距离应大于所需的测量范围。这些措施可为同类装置液位仪表的设计或操作提供参考或帮助。
前言
仪表及自动化技术在炼油化工装置中起着越来越重要的作用,液位测量及控制是自动化技术的重要组成部分。准确可靠的液位测量对装置的平稳运行及安全生产起着十分重要的作用。本文通过引用四个具体案例即抽余液分馏塔开车引发的爆炸、溶剂回收塔操作不稳定、锅炉汽包液位控制不稳定、分液罐玻璃板液位计读数不准确详细说明了生产过程中假液位对装置操作带来的危害,分析了这些假液位产生的原因,并提出了相应的处理措施。
2抽余液分馏塔开车引发的爆炸
2005年3月23日13时20分左右,英国石油公司(BP)在美国得克萨斯州(Texas)炼油厂的异构化装置发生爆炸事故。爆炸冲击波摧毁了附近50个大型化学品储罐,震碎了约1.21km外的居民窗户玻璃,并造成15名工人死亡,180余人受伤及15亿美元以上的经济损失,这是近20年来,美国发生的#严重的工业事故[1~4]。
2.1原因分析
异构化装置的抽余液分馏塔工艺流程如图1所示,该塔在检修完毕后重新开工进料。开车过程中,操作人员用泵将抽余油升压后送至一台内径为3.8m、高度为51.8m的抽余油分馏塔,用于将抽余油分离成轻石脑油和重石脑油组分。由于塔釜出料线上的差压流量计未进行零点校准,在不断关小直至完全关闭塔釜出料控制阀后,相关仪表仍显示塔釜有较大的出料量,因而操作人员误认为该控制阀内漏严重而将其关闭,此时该塔仍在连续进料,但仪表显示液位不上涨,实际情况是塔内液位不断上涨,当液体上升至重沸炉气液两相返塔口位置时,重沸炉返塔气体将大量液体携带到上层塔板上引发严重的雾沫夹带和液泛,当液体继续上升至塔顶后则从气相馏出线上流出。
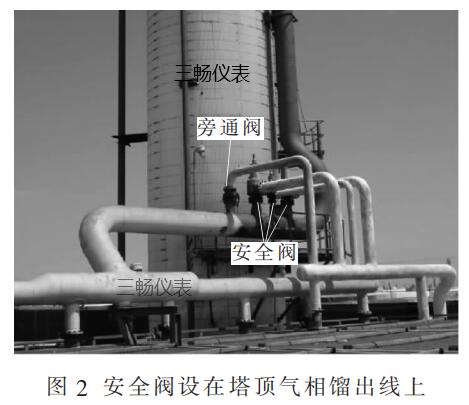
该塔安全阀未设在塔顶封头上,而是设在了距塔顶以下约45.1m的气相馏出线低点处(见图2),大量液体从气相馏出线垂直向下流动,在安全阀入口处产生了额外的静压差,造成该处压力由144.8kPa迅速上升至441.3kPa,超过安全阀定压而导致3个并联的安全阀全部起跳,将气液混合物泄放至一台预先设置的放空分液罐中。放空分液罐的作用是对泄放介质进行气液分离,分出的气体直接被排至大气,分出的液体自罐底通过倒U型密封管排至压力约为20kPa的污油总管中,但这些处于饱和状态的液体沿密封管向上流动时,因静压头损失而产生部分蒸气,蒸气积聚于倒U型密封管顶部形成气阻,使液体不能通过该密封管自流至污油总管中,而只能积聚于放空分液罐内,由于该罐容积有限,液体很快将其充满并沿设在其上方的高度为34.4m的烟囱向外溢出,溢出的液体像喷泉一样向下洒落并蒸发为气体,形成可燃气体蒸气云。该蒸气云被附近一辆没有熄火的小型敞蓬载货卡车发动机引擎的火花点燃而引发了这次大爆炸。
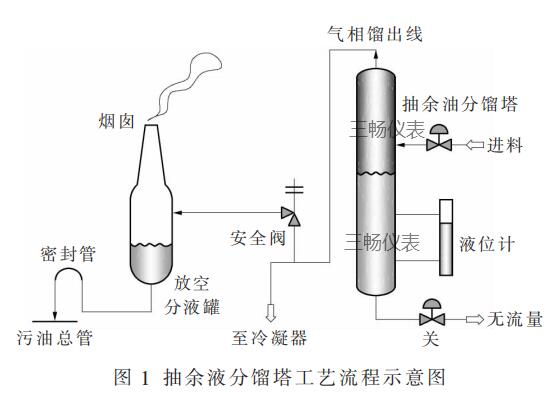
该爆炸是一系列操作和设计失误造成的,如没有按规定的操作程序开车、装满可燃物品的拖车与放空烟囱相距过近、安全阀安装位置过低、安全阀放空介质未密闭排放至火炬系统等[1~6],但操作人员被塔釜液位计显示的虚假液位所蒙蔽是造成该爆炸事故的#主要的原因之一。抽余油分馏塔塔釜选用差压式液位计测量液位。差压液位计的工作原理是容器内液位改变时,由液位产生的静压差也相应变化[7]。两者之间的关系为:
△p=p2-p1=ρ·g·H(1)
式中:△p为液位计下取压口与上取压口间的差压值,Pa;p1为液面以上的上取压口处压力,Pa;p2为液面以下的下取压口处压力,Pa;ρ为被测液体密度,kg/m3;g为重力加速度,在计算时通常取9.81m/s2;H为被测液位高度,m。
在被测液体密度不变的情况下,△p与液位高度H成正比,由测出的静差压△p可计算出被测液位高度H。然而被测液体的密度并不是一成不变的,而是随着进料组成、温度等条件的变化而变化,在一些情况下密度变化较小,由其产生的误差不足以影响装置的正常操作;而在另一些情况下,密度变化较大,由其产生的测量误差非常显著而不能将其忽视。例如,某石油液化气原料的密度对温度变化敏感,0℃时密度为575kg/m3,而30℃时密度变为535kg/m3,相对变化大于7%[8];又如当全塔雾沫夹带产生液泛时,由于液相中存在气泡,气相密度远小于液相密度,导致被测液体密度大幅下降。当差压式液位计以不含气体的液相密度为基准密度,而实际的气液混相密度为原液相密度的65%时,液位计显示液位仅为实际液位的65%。
在开工期间,由于抽余液分馏塔进料密度较设计值低,操作人员开启了进料预热器,使塔釜操作温度进一步提高,温度升高时,介质密度会进一步下降。由于以上两种因素的作用,塔釜液体的实际密度仅为设计值的78%左右,从而造成塔釜显示液位远低于实际液位。根据式(1),当实际液位位于塔釜液位计的上管嘴之上时,无论塔釜液位多高,在上管嘴和下管嘴之间测量的差压△p始终保持恒定且为设计值的78%左右,而液位计显示液位H仍按原设计密度运算得出,故显示的液位一直保持在满量程的约78%处不变,这种虚假液位是导致上述事故发生的主要原因之一。
2.2改进措施在开工阶段或正常操作阶段,应及时通过分析
化验取得因进料或操作条件改变引起的被测液体密度变化情况,然后通过相应的方法修正液位测量的差压信号,从而获得准确的测量液位。
在实际生产过程中,也可采用以下两种方法对虚假液位或起泡进行有效辨别。
2.2.1在塔釜和塔顶间设置差压计
正常操作时每层塔板压降一般不大于0.7kPa,若塔板数为N,则塔釜和塔顶间的压差一般不大于0.7NkPa。在塔釜和塔顶间设差压计,如差压计显示差压突然增加到远大于0.7NkPa且显示液位长时间不发生变化时,则初步怀疑仪表显示液位为虚假液位且塔内实际液位已非常高,此时应加大塔釜出料量并同时减少进料量。如经过一段时间后塔釜显示液位仍无变化,则基本认定显示液位为假液位,需继续加大塔釜出料量、减少进料量并降低重沸器热负荷和回流量,直至液位仪表显示下降为止。在某烷基化装置脱丙烷塔开工过程中,该塔仪表失灵导致操作无法正常进行,开工技术专家于是将一块压力表安装在玻璃板液位计上连接管的放空口上,测出塔底部压力,又从塔顶早已安装好的压力表中读出塔顶部压力,然后由式(1)计算出塔内实际液位已高出玻璃板液位计顶部12.2m,于是立刻采取加大塔釜出料量、减少进料量的措施,直至液位降至正常液位并#终开车成功[6]。
2.2.2在塔釜分段设置玻璃板液位计
如图3所示,在塔釜分段设置玻璃板液位计可用于判定泡沫是否存在。由于玻璃板液位计内的静止液体高度较塔内的泡沫液体高度低,如观察到不同高度且保温良好的多个液位计均有液位但都不是满液位的,就证明了该塔已处于严重的泡沫状态,须进行相应处理[9]。
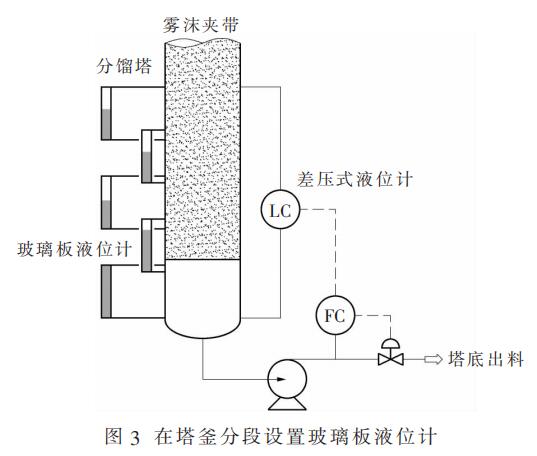
3溶剂回收塔操作不稳定
为提高处理量,某石化厂对其溶剂回收塔进行了改造,改造的主要内容是将单溢流塔板改造为双溢流塔板。改造完成并开工后,发现塔顶回流罐液位极不稳定且塔顶压力难以控制,即使将进料量降至额定量的一半,操作状况也难以改善。当塔底液位上升时,增大塔底重沸器加热蒸汽量或降低塔顶回流量时又会造成回流罐液位急剧升高,于是又开始降低塔底重沸器加热蒸汽用量或增大塔顶回流量,这又造成了新一轮的塔底液位上升,使塔难以在稳定状态下操作[10]。
3.1原因分析
相关技术人员详细对比了改造前、后工艺和仪表管嘴结构及布置情况后,发现塔釜液位计的安装位置是造成上述不正常操作的主要原因。如图4所示,该塔设置了用于将塔釜分为重沸器进料侧和产品出料侧的隔板。改造前,#底层塔盘降液管及液体密封盘在塔的左侧,降液管内液体流入重沸器进料侧,重沸器气液两相在塔的中间位置返塔,且进料管伸入塔内并与降液板和隔板平行,这种设置使重沸器进料管内液体垂直向下流入塔釜,气体也以平行于降液板和隔板向上流动,因而对塔釜液位计造成的影响较小,塔釜液位计可基本反映塔釜的实际液位。改造后,塔板由单溢流变为双溢流,#底层塔盘降液管及液体密封盘、重沸器气液两相返塔口均在塔的中间位置,重沸器气液两相返塔口不再伸入塔内而与塔壁平齐,并在该返塔口处设置防冲挡板,但这种设置使重沸器上升气体与#底层塔盘下降液体逆流接触,造成气体中携带大量液体,这种气液两相物料直接对着塔釜液位计的上部管嘴,导致大量液体通过上部管嘴进入塔釜液位计中[见图5(a)],造成塔釜液位计所测液位为虚假液位且呈锯齿状波动,进而引起重沸蒸汽量、塔顶回流量及回流罐液位的波动,使装置难以平稳操作[10]。
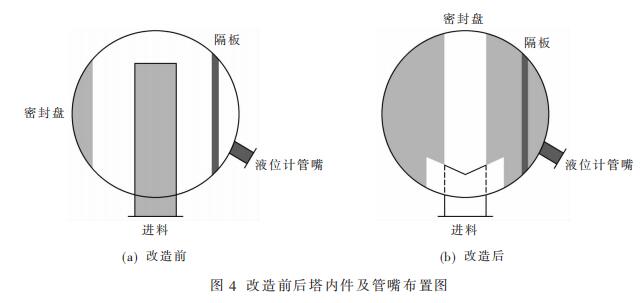
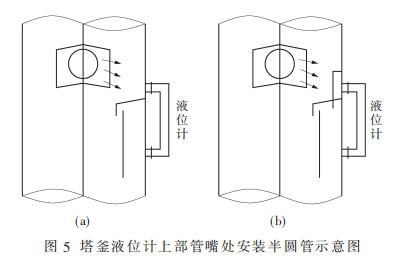
3.2改正措施
塔釜隔板上面的盖板主要用来防止来自#底层塔盘的液体流入塔釜隔板右侧即产品侧。在盖板下方设置新的仪表管嘴是一种有效的改造方案,然而,该方案需在塔体上新增开口,需要的手续繁多且施工强度大,特别是开口部位需要焊后热处理(PWHT)时更是如此。在塔釜液位计的上部管嘴处设置半圆管防冲挡板是一种简单、有效的处理方法。如图5(b)所示,该半圆管可固定在隔板上面的盖板上,用以阻止重沸器气液两相返塔介质通过上部管嘴进入液位计中,使液位计显示塔釜真实液位。
在半圆管上部需设置排气孔。排气孔可设在半圆管的侧壁也可设在顶部挡板处,以尽量降低液体通过该孔流入液位计中为选择依据。当在侧壁开孔时,其结构示意图如图6所示[11]。
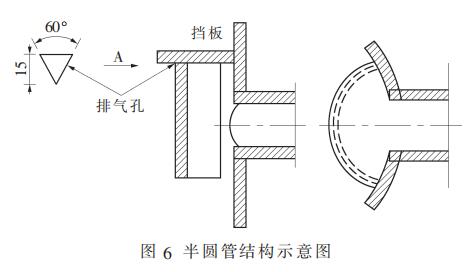
按上述方法改造后,在额定进料条件下塔的操作平稳,产品质量合格,取得了满意的效果。
4锅炉汽包液位控制不稳定
锅炉汽包的主要作用是进行汽水分离和蒸汽净化,蓄存锅炉给水并构成水循环回路。其工作温度和压力可分别高达540℃和25MPa,一旦发生爆炸事故将造成严重后果,故应高度重视锅炉汽包的安全运行和操作。汽包液位是一个极为重要的操作参数,必须将其控制在一定的范围内并保持稳定,否则,当液位过高时,蒸汽携带水滴会损坏过热器管束、汽轮机叶片和其他设备;当液位过低时,会造成锅炉水循环的破坏,容易使水全部汽化烧坏锅炉甚至发生爆炸。汽包液位波动还会影响汽包连续排污系统,#终使蒸汽品质恶化。因此,正确测量并控制汽包液位对确保安全、稳定生产具有重要意义[12~20]。
4.1原因分析
某锅炉汽包采用由锅炉给水量控制汽包液位的单冲量液位调节系统,由于在生产过程中常常存在蒸汽负荷波动等干扰,这些干扰不但会打破汽包内的平衡状态,还会常常造成虚假液位,给控制带来困难。如当蒸汽负荷(蒸汽出料量)增加时,汽包液位本应下降,但由于汽包压力下降,引起水的沸腾加剧,液面以下汽泡量急剧增加,这些汽泡的体积比水的体积大许多倍,结果造成汽包内水发生“肿胀(swell)”现象造成液位升高,但这种升高的液位不代表汽包内储液量的真实情况,所以称其为虚假液位,此时调节器会错误地认为液位测量值升高,从而关小锅炉给水调节阀,减小锅炉给水量,当气泡自液面以下升至水、汽界面后很快就会破裂,导致汽包液位快速下降,即使调节器将大量冷的锅炉水加入到汽包内,由于滞后作用,此时汽包液位不但不上升,反而因水温下降、水面以下气泡快速破灭又进一步下降,直至降到液位危险区,造成事故。可见,仅在汽包上设置单冲量液位调节系统,不能克服以上假液位的影响。
4.2改正措施
采用图7所示的三冲量前馈-串级反馈控制方案可有效地解决上述“假液位”引发的控制问题[12]。
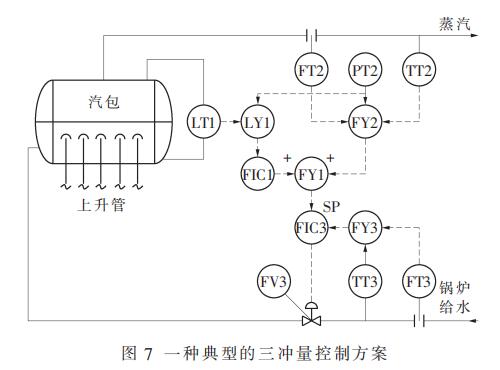
在三冲量控制系统中,主要冲量是汽包液位,辅助冲量是蒸汽负荷和锅炉给水量。汽包液位是反映锅炉汽包工作状态并保证锅炉安全操作的主要工艺指标;蒸汽流量作为前馈信号引入,可降低蒸汽流量扰动对汽包液位的影响,并有效地克服由于假液位现象引起的控制系统误动作;锅炉给水量引入的目的是克服给水自身的扰动对汽包液位的影响。在图7中,主调节器LIC1作用方式为反作用,副调节器FIC3作用方式为正作用,给水调节阀FV3选用气动调节阀,气动执行机构选择气关式。其具体控制过程是:液位控制器LIC1与流量控制器FIC3构成串级调节系统。当汽包液位由于扰动升高时,LIC1的输入为液位测量值与给定值的差值,即LIC1的输入增加,因LIC1的反作用,它的输出下降并进入加法运算器FY1。FY1输出由主调节器LIC1的输出与经FY2进行温度、压力补偿计算出的流量变送器FT2的输出来确定,在蒸汽流量比较稳定的情况下,FT2或FY2的输出基本不变,则加法器FY1的输出减小,由于FY1输出值作为给水流量的给定值,而副调节器FIC3的输入为给水流量的测量值与给定值之差,在给水流量测量值比较稳定的情况下,副调节器的输入增加,由于作用方式为正作用,其输出相应增加,调节阀FV3为气关式,阀开度相应减小,锅炉给水量减少,汽包液位下降,直至回到设定值上达到新的平衡。当蒸汽负荷突然增加,出现了虚假的上升液位时,液位测量值增加,LIC1的输入增加,输出值减小,而相应的流量变送器FT2输出值增加,由于蒸汽负荷作为前馈量,可保证FY1的输出增加,使副调节器FIC3输入减小,因FIC3作用方式为正作用,FIC3输出下降,因此调节阀FV3开度增加,给水流量增加,从而使水、蒸汽保持平衡,使汽包操作不受虚假液位的影响[12~14]。
在该控制系统中,蒸汽流量作为前馈补偿信号,其测量的准确性关系到控制方案的控制品质,因此应选用合适的数学模型,实施温度、压力补偿以保证测量数据的准确。另外,由于温度对锅炉给水的密度影响较大,如水的温度从0℃升至300℃时,其密度从1000kg/m3降至712kg/m3,由此可产生15%以上的测量误差,因此,如锅炉补水的温度变化较大时,其流量也应进行温度补偿[12~18]。
5分液罐玻璃板液位计读数不准确
某油田伴生气凝液回收装置将油田伴生气进行浅冷后送入一台立式分液罐进行气液分离。装置投产后发现分液罐上的玻璃板液位计液位显示不准确,不利于装置平稳运行和安全生产,迫切需要
进行解决。
5.1原因分析
该分液罐上下仪表管口的设置如图8所示。
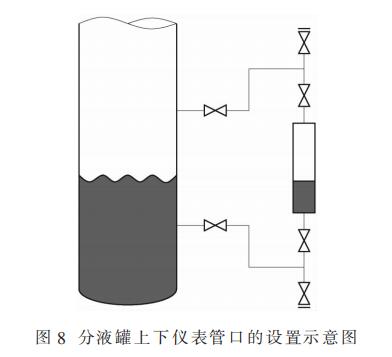
由图8可见,分液罐上下仪表管口之间的距离小于玻璃板液位计的测量量程。当分液罐液位下降至下仪表管口之下时,玻璃板内的液体无法克服下部连接管线的高度差流入至分液罐中,只能被完全隔离在玻璃板液位计中,此时玻璃板液位计中的液位不再与分液罐的实际液位有任何关系,即使分液罐的实际液位接近于0,其所显示虚假液位也保持不变,且读数较实际值高[20],如图9(a)所示。
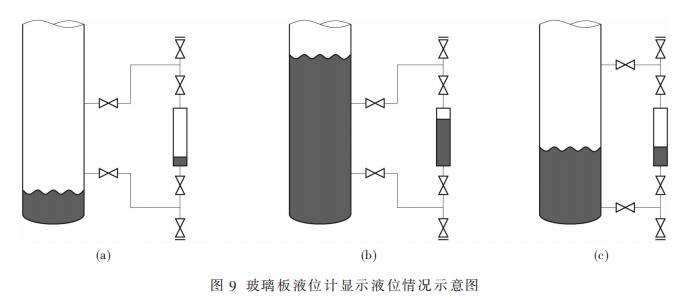
当分液罐液位不断上升,直至升至上仪表管口之上时,玻璃板内的气体被分液罐内的液体完全隔离在玻璃板液位计中。分液罐的液位继续上升时,也只能将玻璃板液位计内的气体进行压缩而不能使其消失,这种结果造成玻璃板液位计显示液位小
于实际液位,如图9(b)所示。
5.2改正措施
如图9(c)所示,改正措施是将分液罐上下仪表管口重新开口,使其之间的距离大于所需的测量范围,且上部连通管必须与上部密度较小的气体连通,下部连通管必须与下部密度较大的液体连通,在两种介质之间没有其他介质。连接管尽量短而直,尽量避免使用过多的弯头等管件[20,21]。
按图9(c)所示方式进行改造后,液位计液位显示正常。
6结语
正确的液位仪表设计需要多专业共同努力,如管道安装专业应注意仪表管口方位是否合理和操作是否方便,设备专业应注意仪表管口与焊缝间距是否满足要求,特别是工艺专业应提出准确的工艺操作条件及影响液位稳定的潜在扰动因素、液位变化对后续工艺过程的影响等,仪表专业根据工艺条件选择#适宜的仪表及控制方法,使其充分发挥作用。在操作过程中,操作人员也应同时具有仪表和工艺方面的相关知识,具有通过各种现象判断出假液位并进行快速、有效处理的能力。
本文通过对4个具体案例进行描述和分析,详细地说明了假液位产生的原因及其对装置操作带来的危害,并提出了相应的处理措施,如在设计时要求玻璃板液位计或差压式液位计上部连通管必须与上部密度较小的介质连通,下部连通管必须与下部密度较大的介质连通;在操作时应及时通过分析化验得到被测液体密度变化情况,然后通过相应的方法修正差压液位计差压信号等。这些措施可为同类装置液位仪表的设计或操作提供参考或有益的帮助。